PROCESS
Process diagram
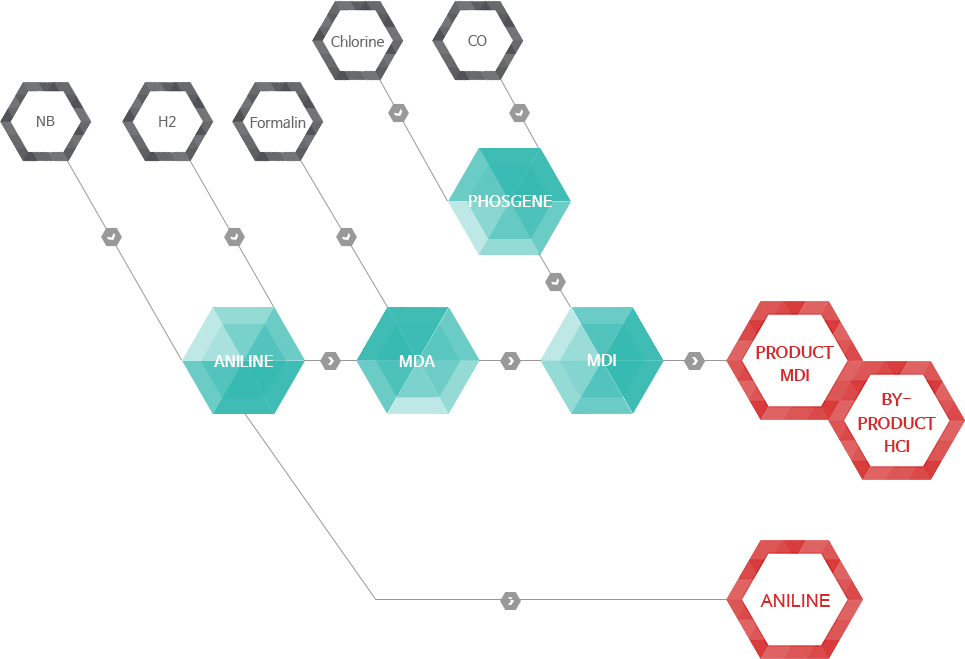
Processes
- ANILINE
PLANT -
A process to produce aniline by using the
Hydrogen from the Hyco plant and nitrobenzene from the MB plantWhen nitrobenzene and hydrogenation catalysts are fed into the reactor and then hydrogen is supplied, aniline and water will be created as a result. The process materials will be vaporized because of the reaction heat. The vaporized process materials will be made liquid by going through cooling and condensation processes and will be divided into water at the top and aniline at the bottom. The aniline at the bottom will go through a drying process to remove a small amount of water content before being produced. Some of the produced aniline will go through the refining process to get higher purity and be sold as a finished product while the rest will be used for making MDA.
- COC
PLANT -
A process to produce carbonyl chloride (COC) by making the carbon monoxide
from the Hyco plant react with the chlorine supplied from outside.COC is generally known as phosgene. When the mixture gas of carbon monoxide and chlorine goes through a reactor that consists of multiple tubes filled with active carbon, COC will be made. At this time, the active carbon will play the role of a COC reaction catalyst. Thus, the produced COC will be pressurized by a compressor before being transferred to the MDI plant.
- MDA
PLANT -
A process to produce methylene diphenyl diamine (MDA) by using the aniline
produced in the aniline plant and the formalin supplied from outside.MDA is the process material prior to MDI, the final product. Formalin will be supplied into the reactor filled with aniline and 35% hydrochloric acid for the reaction process. In this process, 35% hydrochloric acid will work as a catalyst. MDA and hydrochloric acid will be generated from this reaction. In order to remove hydrochloric acid, it is required to go through neutralization and washing processes to separate and produce MDA.
- MDI
PLANT -
A process to produce methylene diphenyl diisocyanate, a final product,
by mixing the MDA produced at the MDA plant and the COC produced
at the COC plant and making them react.In the final process, MDI as well as hydrochloric acid, a by-product, will be produced. When the pressurized and transferred COC is supplied into the reactor filled with MDA, they will react, creating gas of hydrogen chloride and liquid of crude-MDI. The gas of hydrogen chloride will be supplied into a reactor filled with pure water and then the hydrochloric acid containing impurities will go through a refining process to be produced as 35% hydrochloric acid. The liquid of crude-MDI is a mixture of various MDIs with different sizes and molecular weight and will be transferred to the MDI refining plant. Through the evaporator in the MDI refining process, the monomer with the smallest size and molecular weight will be evaporated. After that, recondensation will take place to produce MDI-PH, the final product, while the remaining crude-M, which did not get vaporized, will be produced as MDI-CR, a final product, will also be recondensated.